Tungsten Carbide Button Quality Control
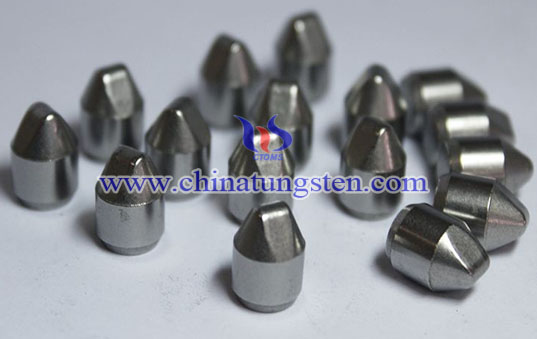
To improve the comprehensive performance and service life of tungsten carbide button, the key is to control the stability of the alloy quality. From the performance of some advanced cemented carbide manufacturers at home and abroad, the alloy composition is basically the same. In order to ensure the quality stability of the ball tooth production process, we should start from the following three aspects.
1. Control the grain size and uniformity of the alloy to avoid coarse crystals. It is necessary to control the grain size and particle size distribution of the raw material WC powder to ensure uniform particle size distribution of the WC powder, and the particle size is similar to the grain size of the alloy. And the control of the grain size of the ball mill can ensure the uniformity of the grain size of the alloy, without coarse crystals, and the quality of the ball teeth can be stabilized.
2. Strictly control the quality fluctuations in the alloy production process, from the traditional rubber process to paraffin, PEG process, easy to accurately control carbon. At the same time, strict control of the storage environment and time of the mixture and the compact, to avoid carbon fluctuations in the production process, affecting product quality.
3. Adopt advanced production process: pressure sintering. Underestimation of alloys, due to the relatively low cobalt content, ordinary hydrogen sintering and vacuum sintering, alloy densification is difficult to achieve the desired goals. The low-pressure sintering method can further improve the densification of the alloy, reduce the inherent microstructure defects of the alloy, further increase the density and strength of the alloy, and increase the wear resistance and fracture toughness of the alloy. At the same time, it is very important to establish a suitable sintering process curve and strictly control the detailed operation of sintering.