Tungsten Carbide Drawing Die Core
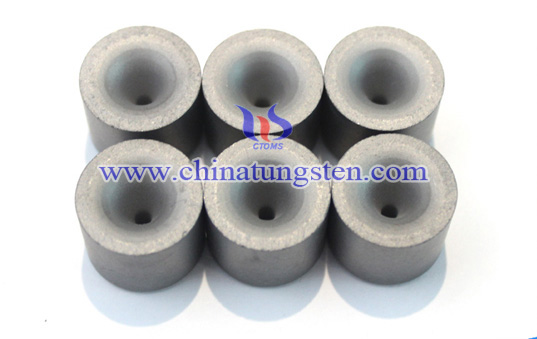
Features
1. No-explosion mold: the raw material tungsten powder with the content of more than 99.95% is used as the main raw material, the impurity content is extremely low, and the mold is not fried;
2, Long service life: the raw material adopts a new formula process, adding wear-resistant element materials, so that the service life of the wire drawing die is greatly improved;
3. Lower processing cost: It is pressed and formed by imported press, sintered by over-pressure sintering furnace, the product has a perforated shape, the tolerance of external dimensions is small, and the processing cost is lower;
4, fast delivery: all types of molds complete, rapid production cycle.
Notes
1. Reasonable choice of mold grade
According to the physical and mechanical properties of the drawn material and the material size, the hard alloy wire drawing die core grade is reasonably selected. For example, in the case of stretching steel bars with a diameter of 20.0 mm or less, wires or bars of non-ferrous metals, YG6 should be selected; for 20-50 mm, YG8 should be selected, and for larger ones, YG11 or YG15 should be selected.
2. Carefully check the wire drawing machine
Before drawing, check whether the stretching machine is stable and there must be no jump, otherwise the drawing die will be easily damaged.
3. Properly clean the wire
Before the wire drawing, the surface of the wire should be properly cleaned, otherwise it is easy to reduce the service life of the die, and it is easy to form scratches on the wire, which affects the surface quality.
4. The correct choice of lubricant
Select lubricants with excellent lubrication, such as brushed powder, to improve the service life of the mold. Good cooling and lubrication of the work area, especially when drawing at high speed, in order to maximize the life of the mold.
5. Reasonable choice of compression ratio
According to the size and performance of the drawn wire, the appropriate compression ratio is selected. If the compression ratio is too small, the production cost is increased, and the compression ratio is too small, which may result in a decrease in the life of the mold, and even a phenomenon of a blow mold may occur.
6. Pay attention to control the surface condition of metal materials
If it is found that the metal particles adhere to the inner hole of the mold during the control process, the surface of the metal material should be stopped immediately, and the adhered metal particles should be removed to polish the inner hole. Carefully clean the metal particles in the die hole before using the mold.
7. Regular inspection of the mold
The most reasonable method is to check the metal particles on the wall of the mold hole regularly and find out the abnormal phenomenon and deal with it in time.
8. Protection of the core of the brushed carbide die
Temporarily unused molds should be protected with anti-rust oil.